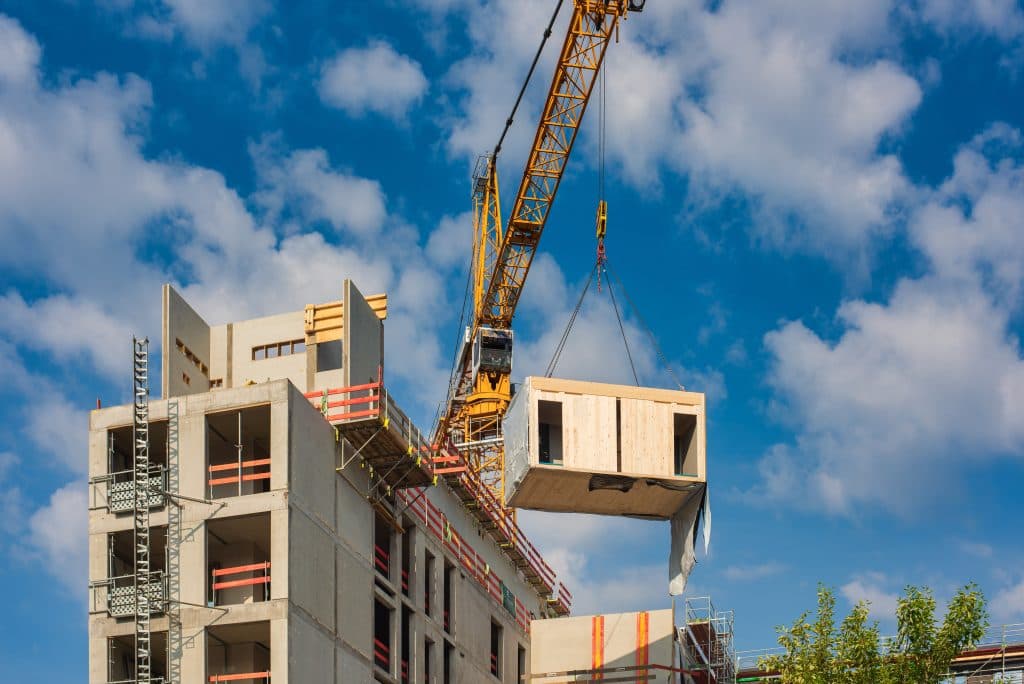
Offsite Construction.

Project Vectors
08 Apr 2024
In recent years, the construction industry has seen a rise in the popularity of offsite construction. This innovative approach to building offers numerous advantages over traditional on-site construction methods. By fabricating components in a controlled factory environment and assembling them at the project site, offsite construction offers increased efficiency, improved quality control, and reduced environmental impact.
Understanding the Basics of Offsite Construction
Before delving into the process, it is essential to define what exactly offsite construction entails. Offsite construction, also known as prefabrication or modular construction, involves the manufacturing of building components away from the project site. These components can include anything from walls and floors to entire rooms or building modules. Once manufactured, these elements are transported to the site and assembled to create the final structure.
Defining Offsite Construction
Offsite construction encompasses a wide range of techniques and methods used to prefabricate building components. This can include modular construction, panelized construction, and volumetric construction. Modular construction involves the manufacturing of complete volumetric units that are ready for assembly on-site. On the other hand, panelized construction involves fabricating wall or floor panels that are then assembled on-site. Volumetric construction combines both modular and panelized techniques, creating larger, more complex modules that can be transported and installed as complete units.
History and Evolution of Offsite Construction
The concept of offsite construction is not entirely new. It has been around for decades but has gained significant traction in recent years. Historically, offsite construction was primarily used for temporary structures or in industries such as healthcare and education. However, advancements in manufacturing technology and increased demand for sustainable and efficient building methods have propelled offsite construction into the mainstream.
One notable example of the evolution of offsite construction is the use of Building Information Modeling (BIM). BIM is a digital representation of the physical and functional characteristics of a building. It allows for the integration of various design and construction disciplines, enabling better coordination and collaboration among project stakeholders. With BIM, offsite construction projects can be visualized and analyzed in a virtual environment before any physical construction takes place, reducing the risk of errors and rework.
Furthermore, offsite construction has also embraced sustainable practices. With the ability to control the manufacturing process in a controlled environment, waste generation can be minimized, and materials can be recycled or repurposed more efficiently. Additionally, offsite construction reduces the environmental impact of construction activities on the project site, such as noise pollution and disruption to the surrounding community.
The Process of Offsite Construction
Now that we have a grasp of the basics, let’s explore the process of offsite construction in more detail. The process typically involves three main stages: pre-construction planning, manufacturing and assembly, and transportation and installation.
Pre-Construction Planning
The pre-construction planning phase is crucial for successful offsite construction projects. During this stage, project teams collaborate to ensure proper coordination between designers, engineers, and manufacturers. Detailed design and specifications are developed, taking into account site limitations, transportation requirements, and regulatory considerations.
Moreover, this stage includes the identification and selection of the most suitable offsite construction techniques for the project. Factors such as project size, complexity, and budget influence the chosen approach. Effective collaboration between all stakeholders is crucial during this phase to align expectations and ensure a smooth transition from design to manufacturing.
One important aspect of pre-construction planning is the consideration of sustainability. Offsite construction offers numerous opportunities for incorporating sustainable practices, such as the use of environmentally friendly materials, energy-efficient designs, and waste reduction strategies. By carefully evaluating these factors during the planning stage, offsite construction projects can contribute to a greener and more sustainable built environment.
Manufacturing and Assembly
Once the design and planning are complete, the manufacturing and assembly stage begins. This phase involves the fabrication of building components in a factory-controlled environment. Skilled workers, aided by advanced machinery, construct wall panels, floor systems, room modules, or even entire building sections.
Quality control measures are implemented throughout the manufacturing process to ensure that each component meets rigorous standards. Inspections, tests, and certifications are carried out to guarantee structural integrity, fire resistance, and thermal performance. By manufacturing offsite, construction companies can achieve consistent quality while minimizing onsite construction time and disruptions.
Furthermore, the manufacturing and assembly stage presents an opportunity for innovation and customization. With the use of advanced technologies such as Building Information Modeling (BIM) and Computer Numerical Control (CNC) machines, offsite construction allows for precise and intricate designs that can be tailored to meet specific project requirements. This level of customization not only enhances the aesthetic appeal of the final structure but also enables efficient use of materials and resources.
Transportation and Installation
Once the components are ready, they are transported to the project site for installation. Careful planning is required to ensure the safe and efficient delivery of these often oversized and heavy elements. Depending on the project’s location and logistical considerations, various transportation modes such as trucks, barges, or trains may be utilized.
On-site, the components are assembled, connected, and integrated to form the final structure. Skilled tradespeople, assisted by lifting and installation equipment, meticulously install the prefabricated elements. The level of coordination required during this phase is significant, as each component needs to fit seamlessly with its counterparts.
Moreover, the transportation and installation stage offers an opportunity to enhance safety and minimize environmental impact. Construction companies employ specialized techniques and equipment to ensure the secure transportation of the prefabricated components, minimizing the risk of damage or accidents. Additionally, the use of efficient installation methods, such as modular construction, can reduce onsite construction time and minimize disruption to the surrounding environment and community.
As we can see, the process of offsite construction involves careful planning, precise manufacturing, and meticulous installation. Each stage presents unique challenges and opportunities for innovation, sustainability, and customization. By embracing offsite construction techniques, the construction industry can revolutionize the way we build, creating structures that are not only efficient and cost-effective but also sustainable and aesthetically pleasing.
Benefits of Offsite Construction
Offsite construction offers several benefits that make it an attractive choice for both construction professionals and clients alike. Let’s explore some of these advantages in more detail.
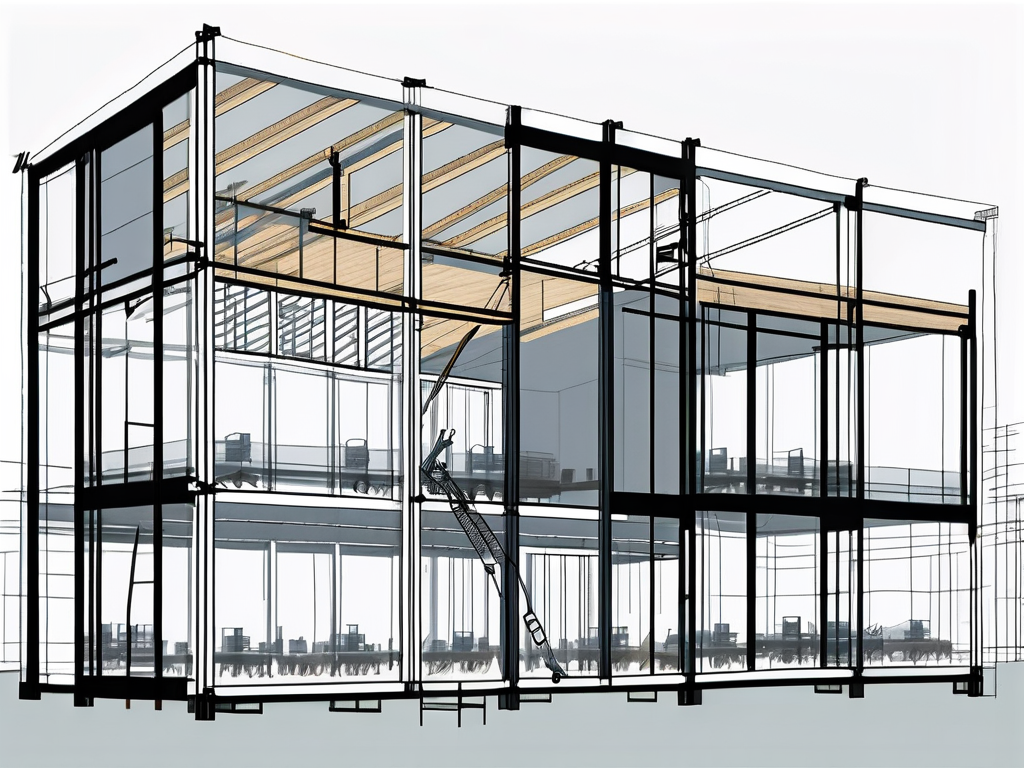
Time and Cost Efficiency
One of the primary advantages of offsite construction is the ability to significantly reduce project timelines. By concurrently manufacturing building components while site preparation occurs, overall construction durations can be shortened. This accelerated timeline translates to cost savings, as labor and other on-site expenses are minimized.
But what does this mean for the construction professionals and clients? Well, for the professionals, it means that they can complete projects faster, allowing them to take on more projects and increase their revenue. For the clients, it means that they can enjoy their finished structures sooner, whether it’s a residential home or a commercial building, and start reaping the benefits of their investment.
Additionally, offsite construction benefits from greater predictability and minimized weather-related delays. The controlled factory environment eliminates weather-related interruptions, ensuring continuous progress without compromising quality. This means that construction projects can stay on schedule, regardless of the weather conditions outside. No more delays due to rain or snow, allowing for a smoother and more efficient construction process.
Quality Control and Consistency
Offsite construction allows for meticulous quality control throughout the manufacturing process. By operating in a controlled environment, production can be closely monitored, and standardized processes can be implemented. This consistency results in higher-quality construction compared to traditional on-site methods.
Imagine a construction process where every step is carefully monitored and every detail is checked for accuracy. That’s what offsite construction offers. With quality control measures in place, construction professionals can ensure that every component is built to the highest standards. This attention to detail not only ensures the structural integrity of the building but also enhances its overall aesthetics.
Furthermore, the use of offsite construction techniques promotes increased precision and accuracy. Production errors that commonly occur on-site, such as incorrect measurements or material waste, can be minimized. This attention to detail ensures that the final structure is both structurally sound and aesthetically pleasing. Clients can have peace of mind knowing that their building is built with precision and will stand the test of time.
Environmental Impact Reduction
As sustainability becomes increasingly important, offsite construction offers significant environmental benefits. By optimizing material usage and reducing waste, offsite construction minimizes the project’s carbon footprint. In addition, the controlled manufacturing environment allows for the implementation of energy-efficient practices and the integration of environmentally friendly materials.
But what does this mean for the environment? Well, it means that offsite construction is a greener alternative to traditional construction methods. By reducing waste and optimizing material usage, less natural resources are consumed, and less waste ends up in landfills. This contributes to the preservation of our planet’s resources and helps combat climate change.
Offsite construction also generates less site-related disturbances and noise pollution, minimizing the impact on neighboring communities. By reducing noise and dust generated by on-site construction activities, offsite construction contributes to a more sustainable and livable environment. Imagine living next to a construction site where noise and dust are constant nuisances. With offsite construction, these disturbances are significantly reduced, creating a more harmonious relationship between construction projects and the surrounding communities.
So, as you can see, offsite construction offers a multitude of benefits that go beyond just time and cost efficiency. It provides meticulous quality control, promotes sustainability, and creates a more pleasant construction experience for everyone involved. It’s no wonder why offsite construction is gaining popularity in the industry.
Challenges and Solutions in Offsite Construction
While offsite construction offers numerous benefits, it also comes with its own set of challenges. Let’s explore some common obstacles and potential solutions in more detail.
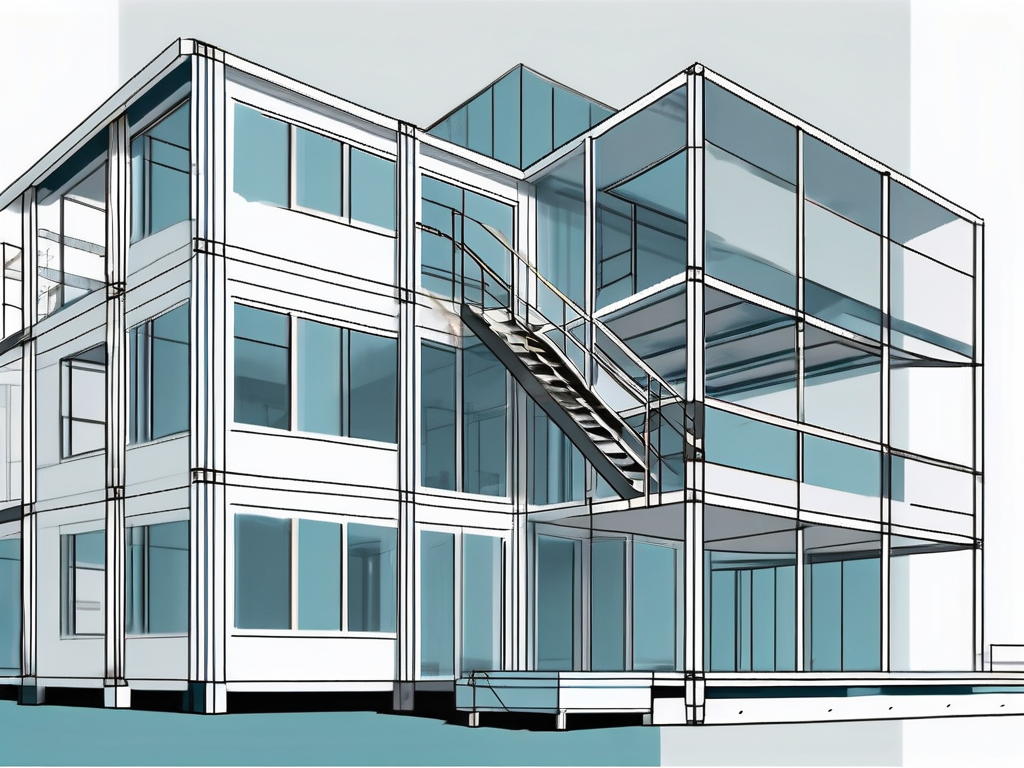
Logistical Issues
Transporting oversized and heavy building components to the project site can present logistical challenges. Ensuring efficient transportation requires thorough planning and coordination with transportation providers. Utilizing appropriate vehicles, adhering to transportation regulations, and selecting the optimal delivery routes are key considerations.
Furthermore, the availability of suitable assembly areas and equipment at the project site must be carefully addressed. Adequate space, cranes, and other lifting mechanisms are required to ensure a seamless installation process.
Regulatory and Compliance Concerns
Offsite construction involves compliance with regulatory requirements both at the local and national levels. Building codes, zoning regulations, and safety standards must be adhered to throughout the project lifecycle. Close collaboration with the relevant authorities and early engagement in the planning process can help ensure that the project aligns with all necessary regulations.
Overcoming Resistance to Change
Resistance to change and the perception of offsite construction as a non-traditional approach can hinder its adoption. Education and awareness campaigns can help dispel misconceptions and highlight the benefits of offsite construction. Sharing success stories and case studies can build confidence among industry professionals and promote a willingness to explore alternative construction methods.
As the construction industry continues to evolve, offsite construction is expected to play an increasingly significant role. By embracing these innovative techniques, construction professionals can deliver projects more efficiently, improve quality control, and reduce the environmental impact of their work. With proper planning, collaboration, and awareness, offsite construction can revolutionize the way we build and shape our world.