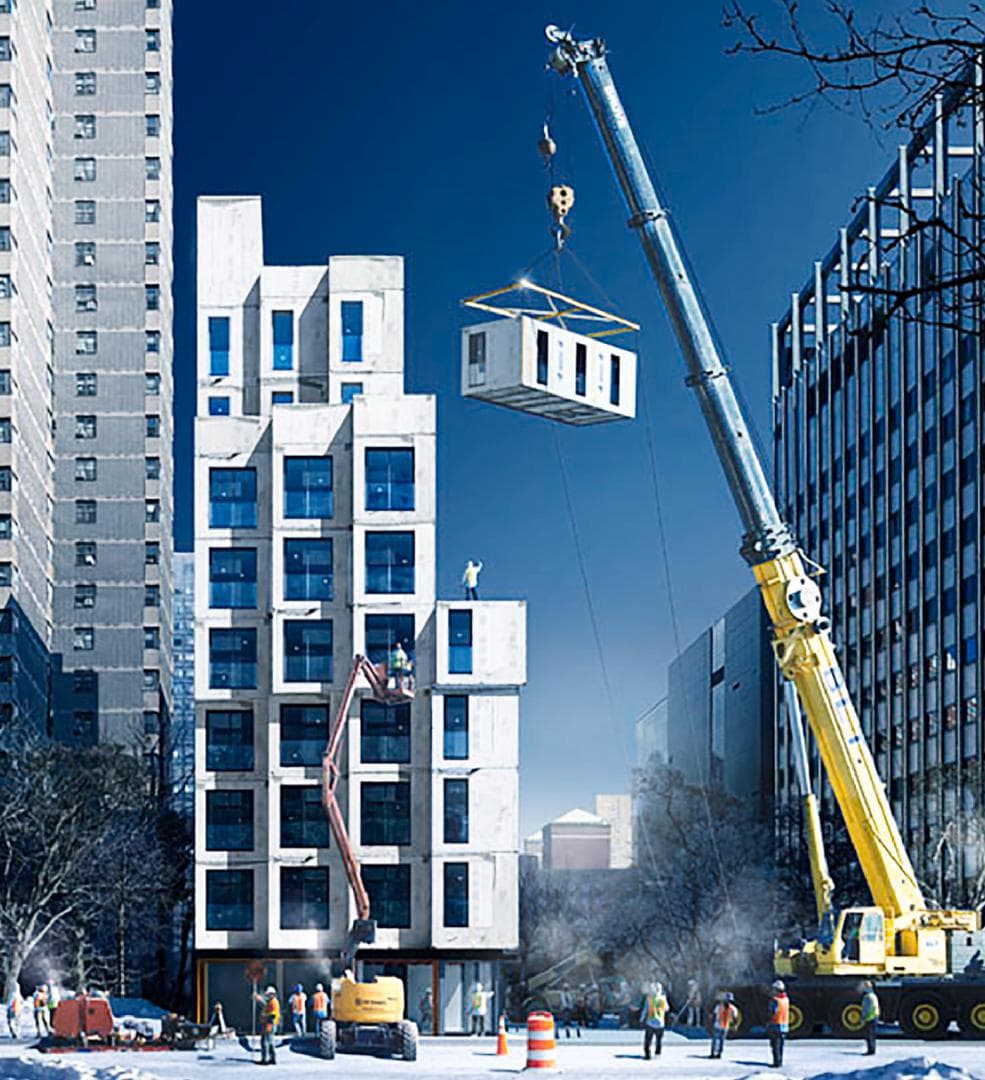
Prefabricated and Modular High-Rises

Project Vectors
23 May 2024
Prefabricated and modular construction is revolutionizing the way high-rises are built. This innovative approach combines off-site manufacturing and on-site assembly to create efficient and sustainable structures. In this article, we will explore the concept of prefabrication and modular construction, the evolution of high-rise buildings, the construction process, the benefits of this construction method, as well as the challenges faced and the solutions that have been developed.
Understanding Prefabrication and Modular Construction
Prefabrication involves the manufacturing of building components at a separate facility, while modular construction refers to the construction of individual modules that are then assembled on-site. These two techniques work hand in hand to streamline the construction process, improve efficiency, and reduce the overall project timeline.
The Basics of Prefabrication
Prefabrication involves fabricating building elements in a controlled environment, away from the construction site. This allows for precise and accurate production, minimizing errors and waste. Additionally, the use of prefabrication reduces on-site labor requirements and the associated risks.
One of the key advantages of prefabrication is the ability to leverage economies of scale. By producing building components in a dedicated facility, manufacturers can optimize their processes and reduce costs. This cost-effectiveness can lead to overall savings for construction projects, making prefabrication an attractive option for developers looking to maximize efficiency.
The Concept of Modular Construction
Modular construction focuses on constructing individual modules that can be easily transported and assembled on-site. These modules can range from bathroom pods to complete living units, depending on the project requirements. Modular construction offers flexibility and speed, as modules can be fabricated simultaneously with on-site preparations.
Furthermore, modular construction is known for its sustainability benefits. The controlled environment in which modules are built allows for better waste management and material optimization. Additionally, the ability to reuse modules in different configurations or projects promotes a circular economy approach, reducing the environmental impact of construction activities.
The Evolution of Prefabricated and Modular High-Rises
High-rise construction has come a long way since the early days of prefabrication. Let’s take a look at the historical overview and modern developments that have led to the rise of prefabricated and modular high-rises.
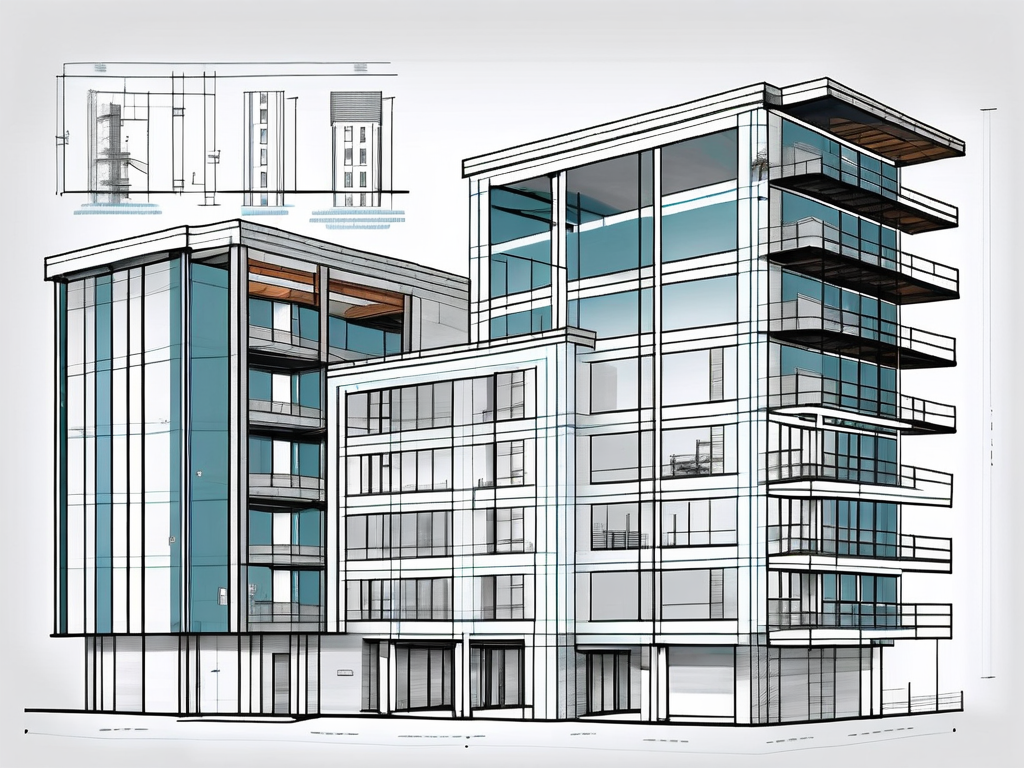
Historical Overview
The concept of prefabrication can be traced back to ancient civilizations such as the Romans and Egyptians, who utilized precast stone blocks for their structures. These early civilizations recognized the benefits of constructing building components off-site and assembling them on location, saving time and resources. Fast forward to the industrial revolution, and we see the mass production of prefabricated elements like cast iron columns and beams, revolutionizing the construction industry.
As technology continued to advance, the development of steel and concrete technologies in the late 19th and early 20th centuries allowed for even larger-scale prefabrication. This shift paved the way for the construction of taller and more complex structures, setting the stage for the modern high-rise buildings we see today.
Modern Developments
In the 20th century, advancements in manufacturing and transportation made prefabrication and modular construction more feasible. High-rise buildings started incorporating prefabricated components, such as curtain walls and floor slabs, to streamline the construction process and improve efficiency. The ability to fabricate building elements in a controlled factory environment not only increased quality control but also reduced construction waste and shortened project timelines.
With the introduction of computer-aided design (CAD) and Building Information Modeling (BIM), the precision and efficiency of the manufacturing process improved significantly. Architects and engineers could now create intricate designs and simulate construction processes virtually, ensuring that prefabricated components fit together seamlessly on-site. This digital revolution in construction technology has further propelled the popularity of prefabricated and modular construction in the high-rise sector, offering endless possibilities for innovative and sustainable building solutions.
The Construction Process of Prefabricated and Modular High-Rises
The construction process of prefabricated and modular high-rises can be divided into three main stages: design and planning, manufacturing and assembly, and installation and finishing. Let’s explore each stage in detail.
Design and Planning
A well-planned design is crucial for a successful prefabrication and modular construction project. Architects, engineers, and manufacturers collaborate to create detailed designs and 3D models. These models help optimize the manufacturing process and ensure the smooth assembly of modules on-site.
During the design and planning stage, sustainability and energy efficiency are key considerations. Designers incorporate green building practices, such as passive solar design and energy-efficient materials, to reduce the environmental impact of the high-rise. Additionally, factors like seismic resilience and wind load resistance are carefully analyzed to ensure the structural integrity of the building.
Manufacturing and Assembly
Once the design is finalized, the manufacturing process begins. Components and modules are fabricated off-site in controlled factory environments using advanced machinery. Quality control measures are implemented at every stage to guarantee precision and adherence to specifications. Meanwhile, on-site preparations are made, such as the construction of foundation systems.
Advanced technology plays a significant role in the manufacturing process of prefabricated high-rises. Automated robotic systems are used to cut, weld, and assemble components with high precision, increasing efficiency and reducing production time. This integration of technology not only improves the quality of the modules but also enhances worker safety in the factory environment.
Installation and Finishing
Once the modules are ready, they are transported to the construction site for assembly. Highly skilled workers carry out the installation, connecting the modules and integrating services such as electrical and plumbing systems. Finally, the finishing touches are added, including interior design elements and facade treatments.
Efficient logistics management is crucial during the installation stage of prefabricated high-rises. Coordination between transportation teams, crane operators, and on-site supervisors is essential to ensure the timely delivery and placement of modules. Additionally, safety protocols are strictly followed to protect both the workers and the structural integrity of the building during the assembly process.
Benefits of Prefabricated and Modular High-Rises
Prefabricated and modular high-rises offer numerous advantages over traditional construction methods. Let’s explore the key benefits that make this approach increasingly popular in the industry.
One significant advantage of prefabricated and modular high-rises is the enhanced quality control during the manufacturing process. In a controlled factory setting, each component can be meticulously inspected and tested to ensure it meets the highest standards. This attention to detail results in a final product that is not only structurally sound but also aesthetically pleasing.
Efficiency and Speed
The off-site production of building components allows for simultaneous on-site preparations, resulting in a significantly faster construction timeline. Prefabrication and modular construction also minimize on-site disruptions, reducing labor and material waste.
Moreover, prefabricated and modular high-rises offer greater design flexibility. Architects and developers can choose from a wide range of customizable options to create unique and innovative structures. This flexibility allows for creative freedom while still maintaining the efficiency and speed benefits of this construction approach.
Environmental Impact
Sustainability is a growing concern in the construction industry. Prefabrication and modular construction help minimize waste by optimizing material usage and reducing transportation-related emissions. Additionally, the controlled manufacturing environment allows for efficient energy usage and the incorporation of eco-friendly technologies.
Furthermore, prefabricated and modular high-rises often have a smaller environmental footprint compared to traditional construction methods. The precision engineering and material optimization inherent in this approach result in less construction waste and a reduced impact on the surrounding environment.
Cost-Effectiveness
Prefabrication and modular construction can offer cost savings compared to traditional construction methods. By streamlining the construction process, labor costs are reduced. Additionally, the off-site production allows for better cost control and material optimization.
When considering the long-term benefits of prefabricated and modular high-rises, it becomes clear why this construction approach is gaining popularity in the industry. From efficiency and speed to environmental sustainability and cost-effectiveness, the advantages of prefabrication and modular construction are shaping the future of urban development.
Challenges and Solutions in Prefabricated and Modular Construction
While prefabrication and modular construction bring numerous benefits, they also come with their own set of challenges. Let’s explore some of the challenges faced in this industry and the innovative solutions that have been developed.
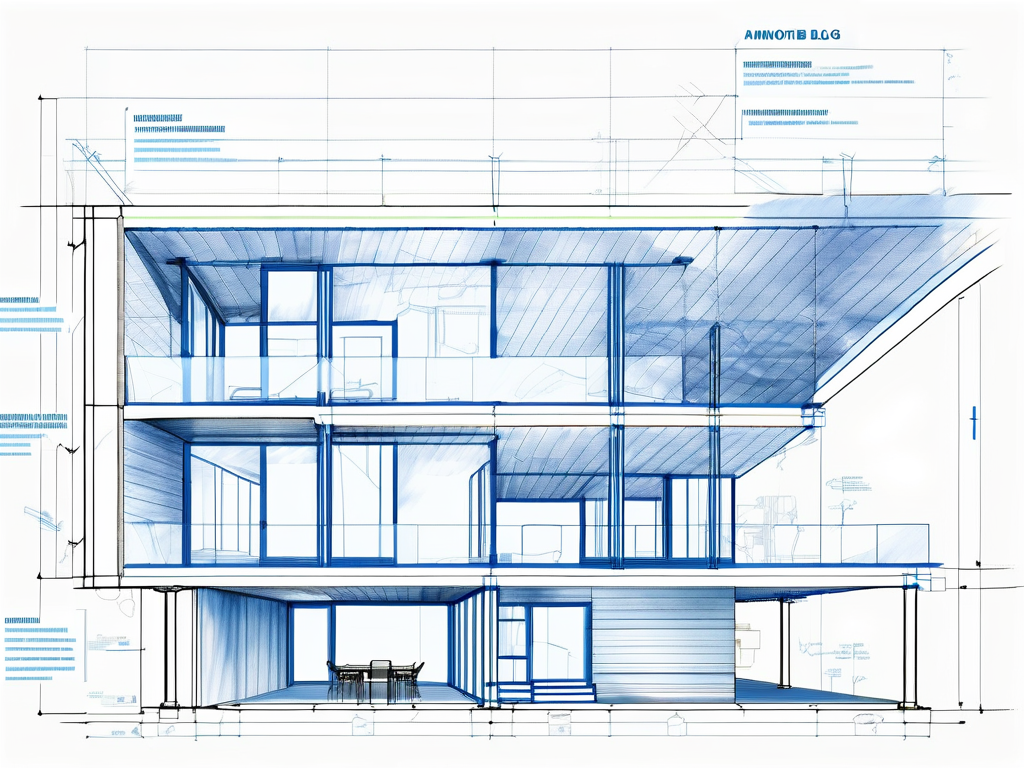
Logistical Challenges
The transportation and delivery of large modules require careful planning and coordination. The size and weight of modules, as well as the availability of infrastructure and suitable routes, pose logistical challenges. However, innovative practices such as modular stacking and the use of specialized transportation methods have been developed to overcome these obstacles.
Modular stacking involves arranging modules in a way that maximizes space utilization during transportation. This not only reduces the number of trips required but also ensures that modules are securely fastened, minimizing the risk of damage during transit. Specialized transportation methods, such as self-propelled modular transporters (SPMTs), have also emerged as a solution. These vehicles are equipped with hydraulic systems that allow for precise control and maneuverability, enabling the transportation of large and heavy modules with ease.
Regulatory Hurdles
The adoption of prefabrication and modular construction often requires regulatory approval and the adaptation of building codes and standards. Educating regulatory authorities and incorporating modular construction guidelines into local codes have been key solutions in overcoming these hurdles. Furthermore, collaboration between industry professionals and policymakers has helped drive advancements in this field.
Efforts to educate regulatory authorities about the benefits and safety standards of prefabricated and modular construction have been crucial in gaining their approval. This includes providing comprehensive documentation, case studies, and conducting workshops to showcase successful projects. In addition, industry professionals have actively collaborated with policymakers to develop guidelines that specifically address the unique requirements of modular construction. This collaborative approach ensures that regulations are not only met but also adapted to support the growth of this innovative construction method.
Innovative Solutions
The industry continues to innovate and develop new solutions to further improve the prefabrication and modular construction process. Technological advancements, such as the use of robotics and automation, help optimize manufacturing processes and increase precision. Additionally, research and development efforts focus on improving module design and integration, as well as exploring new materials and sustainable practices.
Robotic systems have revolutionized the manufacturing process by automating repetitive tasks, reducing human error, and increasing productivity. These systems can perform tasks such as cutting, welding, and assembling modules with high precision and efficiency. Furthermore, ongoing research and development efforts are dedicated to enhancing module design and integration. This includes the development of standardized connectors and interfaces that allow for seamless integration of modules, reducing construction time and improving overall quality.
As the industry evolves, it is clear that prefabricated and modular construction will continue to play a significant role in shaping the future of high-rises. The combination of off-site manufacturing and on-site assembly offers efficiency, sustainability, and cost-effectiveness. Although challenges exist, innovative solutions continue to be developed, driving the growth and use of this construction method.